When we think of manual work, the image of someone lifting heavy furniture or construction materials comes to mind, but manual handling includes far more jobs than just these. Even people working in jobs that are largely sedentary sitting at a workstation most of the day may undertake some manual handling tasks that pose risks.
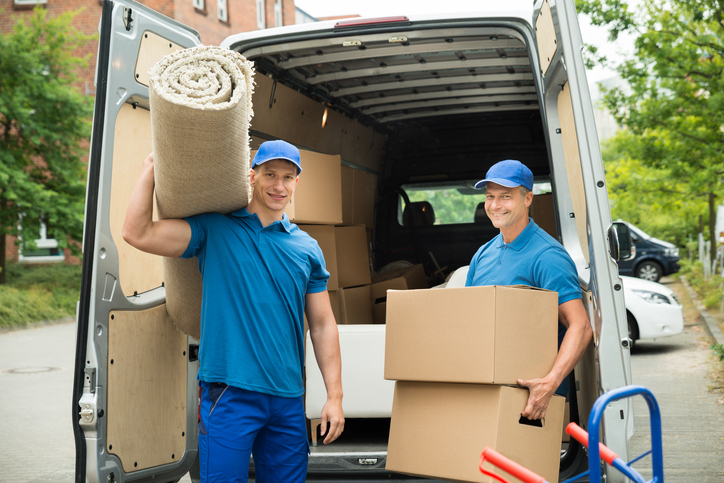
What is Manual Handling?
Manual handling is any work involving an effort to lift, pull, push, carry, hold or restrain an object or person.
When Manual Handling becomes Hazardous?
Any employee who completes manual handling tasks on an ad hoc or regular basis are at risk of injury and need protection from the risks. At the same time, you will be protecting your business by complying with your obligations as an employer to provide a safe work environment.
Injuries such as sprains, strains, lower back pain, soft-tissue injuries to wrists, arms, shoulders, neck or legs can be the result of hazardous manual handling. Known as musculoskeletal disorders (MSDs) they can impact on quality of life and the ability to continue working. Hazardous manual handling that can lead to these injuries may include:
- repetitive or sustained application of force, awkward posture or movements
- tasks that are difficult due to a high force applied
- continuous vibration
- manual handling of live people or animals
- handling of unstable loads that are difficult to grasp or hold.
Worksafe Requirements
Worksafe requires all employers in Australia to provide a safe workplace which includes identifying tasks that involve manual handling. If tasks pose the risk of a musculoskeletal disorder you must eliminate the risk by:
- changing the workplace layout, environment or systems
- changing the objects used in the task
- using mechanical aids.
Where it is not practical to eliminate the risk, you are required to provide information, training or instruction to your workers. If there is a change or a report of an MSD you must conduct a review and revise your risk controls.
Minimising Risk of Injury
An audit of your workplace by an Exercise Physiologist or Occupational Therapist can identify risks posed by manual handling and other tasks. Often employers and employees are not even aware of the risks if a task is a routine part of their day. An audit may help you to see the risks and ensure you are complying with legislative requirements.
During an audit, information is gathered via a structured interview and worksite inspection. The audit can take place at any stage of business development. This information is then used to develop strategies to minimise the risk of injury and harm to people in the workplace. An occupational safety and health management system is then implemented as a planned, documented way of reducing the hazards of manual handling.
Training Can Help
Not only can risks be hard to identify when you do your job day in day out, but it can also be hard to change the way you undertake manual handling. Years of doing something one way can take training to break the habit. Being shown how to use a piece of equipment by a colleague is not adequate training if that colleague didn’t receive proper training or has forgotten. Following adequate training, you can then expect your workers to:
- use manual handling equipment properly
- follow workplace policies and procedures (e.g. using trolleys, not lifting on their own)
- attend follow-up health and safety training
- not take any shortcuts that could increase the risks.
If you have any questions about manual handling and the risks it may pose to your employees, contact one of our experienced Exercise Physiologists or Occupational Therapists by calling (08) 9388 9000 1300 307 912 or send us an enquiry and we’ll get back to you with the information you require.